|B3RNY|
Well-Known Member
(Note: Please read the entire post before you begin.)
Let me start by first apologizing for producing yet another D.I.Y. carbon filter, I'm terribly sorry but most of the other do-it-yourself filter tutorials I've found are lacking something (usually they're just unorganized & constructed poorly.) Carbon filters are much more affordable than they used to be, so constructing your own may not always save you money.
I also wanted to stress the importance of odor control, as well as the effectiveness of activated carbon air scrubbers to those new in the field (or those who are skeptical); as long as an adequate amount of activated carbon & the proper sized extraction fan are used in combination, a carbon filter will keep all odors contained inside of the room in which it operates. Activated carbon can remove about 99.9% of airborne particles.
Before you begin building anything, it is very important to figure out the right dimensions (& fan size) for your application, or else the filter will not work as efficiently. This tutorial can be used as a rough guideline to build/modify your own carbon filter creation. Multiply Length X Width X Height = Volume (in Feet) to figure out what size fan you will need- inline fans are rated in C.F.M.'s (Cubic Feet Per Minute.) In an ideal setting, a grow room exhaust fan would exchange all of the air in the room 2-3 times per minute (removes odors & can lower temperatures); it's your choice but I recommend that you use a fan that can move all of the air in the room once every 5 minutes, as a minimum (removes odors.) Typically one would use a 4" fan on a small room or closet, a 6" fan on a bigger space and an 8"+ (or even multiple 6" fans) for a large room; those measurements refer to the diameter of the fan's flange- bigger fans usually move more air = higher C.F.M. rating. Invest in the highest quality fan that you can afford.
I borrowed (& modified) this guide from another thread but it is quite useful. If your C.F.M. rating is not listed then choose the C.F.M. rating that is the closest to your own, divide by the corresponding height (example: 200 C.F.M./12= 16.6.) Then divide your C.F.M. rating by the resulting number (16.6) to figure your recommended core height. I recommend that you use the following diameters as closely as possible: for <220 C.F.M. = 4”; 221-475 C.F.M. = 6”; 476-600 C.F.M. = 8”; >600 = 10”… I also recommend that you use a carbon thickness of at least 2”, by using a shell diameter 2” wider than your core diameter.
It's better to use a fan/filter combo that's too large, rather than one too small.
Legend:
D = Inner Core Diameter (In Inches)
H = Filter's Height (In Inches)
IC = Inner Core (Surface Area- Inches Squared)
C.F.M.|D |H | IC |
150 |4 | 9 |113 |= (CFM/Height= 16.6)
200 |4 |12|151 |= (CFM/Height= 16.6)
275 |6 |12|226 |= (CFM/Height= 22.91)
375 |6 |16|302 |= (CFM/Height= 23.43)
400 |6 |24|603 |= (CFM/Height= 16.6)
550 |8 |24|603 |= (CFM/Height= 22.91)
650 |10|24|754 |= (CFM/Height= 27)
Gather supplies...
Materials Needed:
Hardware Store:
*Duct Tape (Duh.)
*Metal Snips or Strong Scissors
*Small (4") Ducting End Cap
*Large (6") Ducting End Cap
*1 6"-4" Duct Reducer
*1 4" Duct Collar
*1 Roll 1/4" Hardware Cloth (Stronger Than Wire Mesh (Which Will Sag))
*2 4" Hose Clamps
*2 6" Hose Clamps
Department Store:
*Plenty of Activated Carbon (Pet/Aquarium Isle)
*Pantyhose (Preferably New)
*Quilt Batting Material
*4" Flexible Ducting
*Inline Fan, extractor or Duct Booster-Fan
*A Couple O' Tools (A Flat Head Screwdriver is Required for the Hose Clamps)
1. Stay Organized...
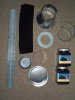
(Pictured: Clockwise from left- 1/4" Wire Mesh, Black Pantyhose, 6"-4" Duct Reducer, 6" & 4" Hose Clamps, 2 Jars of Activated Carbon, 6" Duct Cap, 4" Duct Cap, 4" Duct Collar, Duct Tape)
2. Cut some wire mesh as wide as the desired length of your filter (mine will be 12"), as long as the circumference of your large duct cap (4” fan = 12.5, 6” = 19, 8” = 25, 10” = 31.5 (circumference in inches)), plus 1 inch. It’ll be easier if you make this cut against the curl of the wire mesh, because it will help if you use the natural curve of the mesh to wrap it around the large duct cap, forming a cylinder as in the picture (the outer shell of the carbon filter.) Don’t forget to cut it a little long; you need it to overlap so that you can secure it together. You can even double wrap the mesh to make a stronger filter, but it will hold up nice & sturdy regardless. Secure the cylinder to the end cap with a hose clamp, hold the other end in its cylindrical form and use thin wire, string or the wiry edges of the wire mesh to secure the wire mesh in its cylindrical form. I fastened my cylinder in place using the wire that came laced through the wire mesh (to keep it from unraveling), by weaving it tightly through the overlapped edge. Throughout the entire process, focus on wrapping & securing everything neatly & tightly, with good, clean edges. Leave the other end open for now, (use my photos for reference; I apologize, I didn’t take as many pictures as I would have liked.)
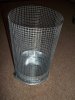
(Outer Shell)
3. Use the same method to cut some wire mesh for the inner cylinder. Cut it to length (the length of your filter (12”

Your core should look something like this:
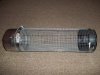
(The Inner Core)
4. Insert the duct collar on the inner cylinder into the inside of the duct reducer and stuff the inside with the cotton/quilt batting around 2" or so thick (until it is level/flush with the 4" duct collar… this is where the air flow will begin& the material will help keep the carbon granules in place.) Now rest assured, the most labor-intensive part is over.
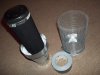
(Carbon Filter Core, Outer Shell & Duct Tape)
5. Now that both of the major parts of the carbon filter are made, you can fit them together. Slide the open side of the 6" shell over the 6" side of the reducer and use the last 6" hose clamp to fasten them together. This should give you a carbon filter frame that resembles something of this nature:

(Completed Carbon Filter Body)
6. Now to fill (and refill) your carbon filter, simply loosen the hose clamp on the bottom of the filter, remove the duct cap and pour activated carbon on top of the quilt batting in-between the 2 mesh cylinders, stopping about 1.5" before it is full and fill the rest with more quilt batting/material to keep the carbon granules from moving around/falling out. I made a 'pre-filter' by cutting a strip of the quilt batting material to wrap around the outside of the filter, beneath the hose clamps. It will make the filter look a little more professional and will filter out large particles in the air, making your carbon last longer (extra pantyhose can be used here in place of the batting.)
You can caulk the inside of the filter where the duct reducer meets the 4" collar to make a good seal, ensuring your carbon is being used efficiently. I caulked all of the seals on my filter, except the end that needs to be removed for refilling. Another good tip is to put a strip of duct tape around each cylinder end, beneath the hose clamps so that they (the hose clamps) don't bend/distort the wire mesh cylinders too bad... it also seems to make them more solid & reduce noise/vibration.
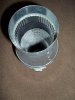
(A Look Inside of The Finished Filter)
Here's a look at the final product, ready to be strapped to an exhaust fan and cranked up. Here you can see how the duct tape was used beneath the hose clamps. Even though only the carbon between the strips of tape on each end is being used efficiently- she still served her purpose well. Just like a name brand carbon filter, the first time you start it up (& after refilling- it will blow out a little carbon dust.)
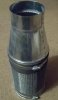
(Voila!)
A refining touch: when my filter was finished, I later went back and took it all apart to modify it a little bit. I wrapped another piece of wire mesh around the inner core & the outer shell, so that each pair of pantyhose had 1 layer of wire mesh on each side of it... this greatly improved the structural integrity of the filter itself and helped hold the pantyhose in place.
Make sure to complete each step as neatly & tightly as possible to get the best results. If you use a fan that is to small- the motor will burn out more quickly, if your fan is too large the carbon will be used up too quickly (& not nearly as efficiently.) Carbon can be found in large quantities on auctions sites, such as eBay.
I built this filter several years ago. At the time, I was using a 4" 80 C.F.M. duct booster fan but I knew that I was going to upgrade that so I built my filter to such a dimension/carbon thickness that it would allow for such an upgrade without complications (which is why I strayed a bit from the guidelines given.)
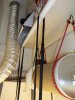
(It's better to pull air through you filter than to push it.)
"...where credit is due", this is the tutorial that inspired my creation:
http://www.icmag.com/ic/showthread.php?t=31679
(from a guy named DurbanPoison, he took more pictures and made a nice tutorial as well though the final product was a bit sloppy in appearance.)