And those are about , the two pcbs I need for my version of GD-SDS box ...
(in a corner of A4 sized page )
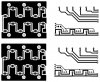
(led thermal pad connection spokes to copper pour ,are missing )
The smaller -easy- one is made with FR4 ...One piece per box ....
The other one -the really tricky one- has to be made x3 times ...
And is MCPCB ..
Thermal transferring the printed circuit ,doesn't worry me that much ...
Soldering the tiny SSLs with "hot-plating " doesn't worry me either ....
What worries me ,is the soft ally and the chemical copper etching agents ...
Not good combo ,there ...
I keep thinking ....
Alum chemical Isolation ...
Covering with :
Wax,PVA ,silicone,grease, plain acrylic glue...
Even Laser-printer toner powder,as a thick coat ,melted afterwards in kitchen oven forming a solid film ! ...ect...
Need something with the least porosity ...
All of the above resist etching agents ...
And I'm thinking of -if it is enough cheap to do - having them all goldplated,not
for cosmetic reasons ,but for oxidation protection of copper ...
(specially on the leds pcbs ,which have large area of thermal copper pour )...
And of course ,MC-PCB of leds will be cut-off a bit larger in size-before etching- ,so
if any ally is lost at sides ,the
final pcb area will remain intact ,with some light "post- etching trimming " work .....
Also ....Etching here is not done by " diving " the pcb in etching agent ....
Here a small size
plastic soft art brush ,
will help applying
small quantities of the etching agent
carefully at a time ,
on appropriate place,until etching is complete ...
Then with cloth/paper wipe ,etching agent is removed ....
After "hand-crafted" micro-etching the mcpcb ,
a lot of warm water will wash away any etching agents residues ...
Then the ally isolation will be removed ...
Holes opened ...
Size trimmed down,with i.e. a sanding belt machine ...Or with Dremmel cutter (the best tool ever ! ) ...
And move on to gold-plating ,maybe ,before soldering the leds ....
(Hot plating in kitchen or with cloth iron ,high precision temp gauge ,timer
and Reflow soldering time pattern of leds-from pdf- ,really well understood and studied...
And try to follow it as close as possible ...)