noodle-led
Well-Known Member
Or - If the LED light fixture still works, it just doesn't have enough features yet.
I replaced my 2x Vero29 light in my 30"x30" tent with a new Bridgelux EB Series Gen2 build and took the time to implement some new features. On its face I have 9x 560mm strips (5x 3000k, 4x 5000k) run by a HLG-185H-C1050 which can run them at 1100mA for a total of about 210W at the wall. Strips are attached to 24" wide aluminum flashing with 20mm thermal tape with spacing from the center out of 85mm, 83mm, 79mm, 73mm. The two center cross members are 3/4"x3/4"x1/8" aluminum L and the outside frame is 1/2"x1/2"x1/16" which is plenty sturdy for the frame and saved some bucks over using 1/8" for the whole thing which is overkill. The flashing is attached with pop rivets apart from the corners which have M3 screws in them for no good reason.
Because I only grow one plant at a time I don't need the whole 28" wide fixture lit up all the time, especially in veg. I added a switch which simply shorts out 4 of the 3000k strips and consolidates most of the light toward the middle. This drops the voltage from around 190VDC to 95VDC but the important point is that I'm running two circuits of strips on the same single driver. All my strips are in series but this method would work even better on parallel setups where you won't have to worry about keeping the combined voltage in the driver's constant current range-- a 20V driver could have switches that would disable as many of the strips as desired and always put out 20V.
Keen-eyed observers will note I tried cutting some vent holes under the driver. It gets up over 55C in still air when pushing 1100mA and the vent holes maybe lowered the temp 1-2C and I added a spacer to lift the driver away from the sheeting to allow better airflow. The original design had space for one of my Initgnokt wifi far red pucks but I decided I didn't want the wiring of it to get in the way of the lights so I just used some aluminum stars and spaced out the same 4x Cree XP-E 730nm LEDs.
Speaking of the far red LEDs, they are run by a separate 12V power supply that drives them up to 700mA and is controlled via wifi / MQTT, fully 5V PWM dimmable 0-100%. Because I had the controller there anyway, I've also wired in the HLG's dimmer wires with open-collector (~10V) PWM so those are digitally controllable over the wifi (for ramp up/down if desired) as well as able to be overriden by the standard knob on the front we all are familiar with.
Not having enough features yet, I also wired in a DC volt and current meter for instant feedback of power usage. This is wired into the HLG driver's output so there will be no light emitted when the main fixture is off. That is controlled separately by a sonoff relay, but there is an open GPIO on the microcontroller so if someone really wanted to they could also implement an AC relay. I opted to avoid having to deal with mains power. Lastly, I added an environmental sensor, a DHT22 temp/humidity sensor. I wasn't getting very accurate humidity readings so I swapped it for a BME280 in the final version. Eventually I will make a little extension cable for the sensor to move it away from the radiated heat of the light. A 3D printed enclosure (link) holds all the goodies.
Control of the homemade Ebb & Flow system as well as data logging of Temp / Humidity / VPD is run through Node-RED on a Raspberry Pi 2 with a dashboard for at-a-glance status. (sad trombone) You can see the humidity is a little low for my new seedling. The new ventilation system is too powerful even on low speed.
Now grow you little plant, grooooowwww!
I replaced my 2x Vero29 light in my 30"x30" tent with a new Bridgelux EB Series Gen2 build and took the time to implement some new features. On its face I have 9x 560mm strips (5x 3000k, 4x 5000k) run by a HLG-185H-C1050 which can run them at 1100mA for a total of about 210W at the wall. Strips are attached to 24" wide aluminum flashing with 20mm thermal tape with spacing from the center out of 85mm, 83mm, 79mm, 73mm. The two center cross members are 3/4"x3/4"x1/8" aluminum L and the outside frame is 1/2"x1/2"x1/16" which is plenty sturdy for the frame and saved some bucks over using 1/8" for the whole thing which is overkill. The flashing is attached with pop rivets apart from the corners which have M3 screws in them for no good reason.

Because I only grow one plant at a time I don't need the whole 28" wide fixture lit up all the time, especially in veg. I added a switch which simply shorts out 4 of the 3000k strips and consolidates most of the light toward the middle. This drops the voltage from around 190VDC to 95VDC but the important point is that I'm running two circuits of strips on the same single driver. All my strips are in series but this method would work even better on parallel setups where you won't have to worry about keeping the combined voltage in the driver's constant current range-- a 20V driver could have switches that would disable as many of the strips as desired and always put out 20V.
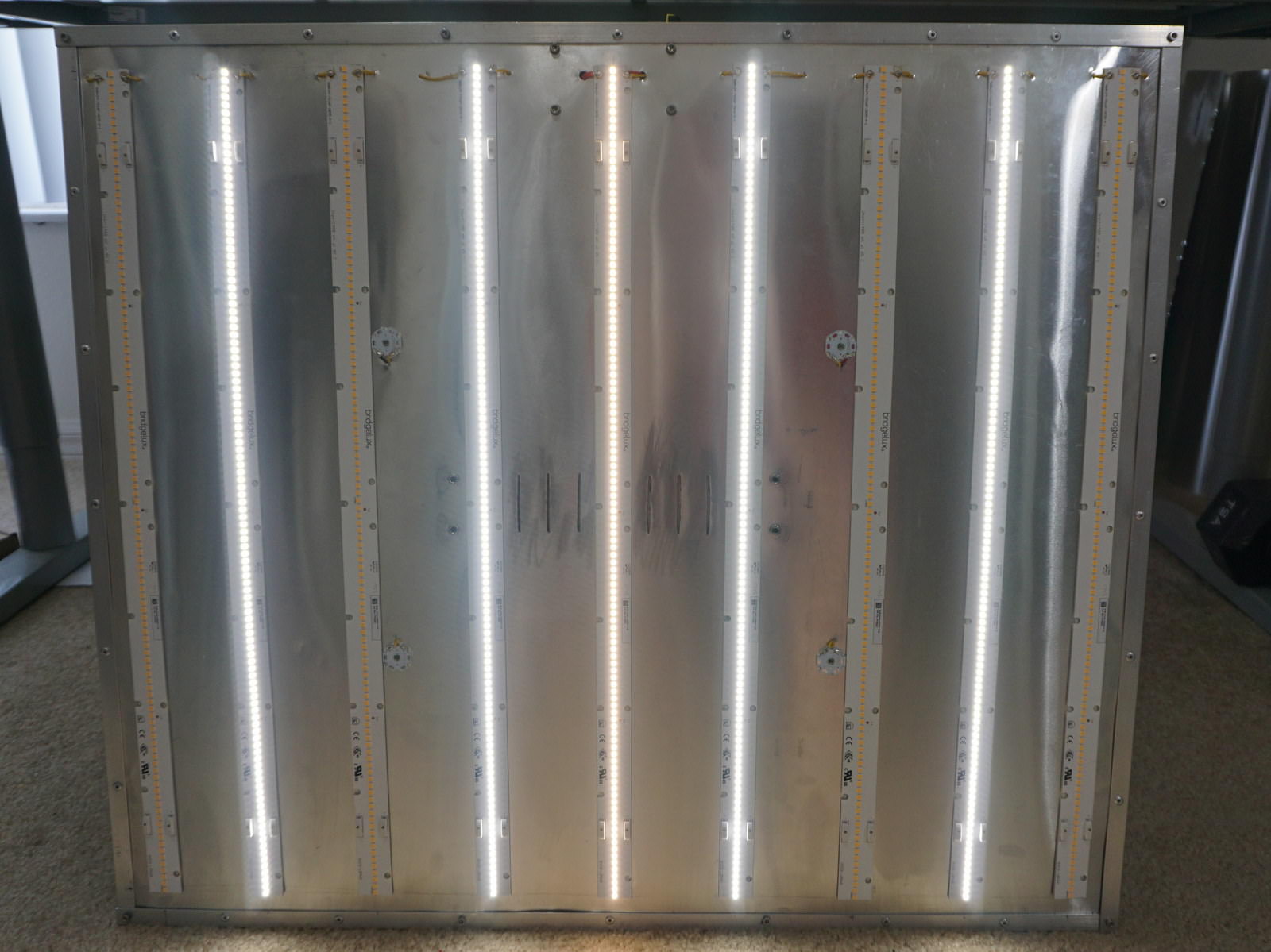
Keen-eyed observers will note I tried cutting some vent holes under the driver. It gets up over 55C in still air when pushing 1100mA and the vent holes maybe lowered the temp 1-2C and I added a spacer to lift the driver away from the sheeting to allow better airflow. The original design had space for one of my Initgnokt wifi far red pucks but I decided I didn't want the wiring of it to get in the way of the lights so I just used some aluminum stars and spaced out the same 4x Cree XP-E 730nm LEDs.

Speaking of the far red LEDs, they are run by a separate 12V power supply that drives them up to 700mA and is controlled via wifi / MQTT, fully 5V PWM dimmable 0-100%. Because I had the controller there anyway, I've also wired in the HLG's dimmer wires with open-collector (~10V) PWM so those are digitally controllable over the wifi (for ramp up/down if desired) as well as able to be overriden by the standard knob on the front we all are familiar with.

Not having enough features yet, I also wired in a DC volt and current meter for instant feedback of power usage. This is wired into the HLG driver's output so there will be no light emitted when the main fixture is off. That is controlled separately by a sonoff relay, but there is an open GPIO on the microcontroller so if someone really wanted to they could also implement an AC relay. I opted to avoid having to deal with mains power. Lastly, I added an environmental sensor, a DHT22 temp/humidity sensor. I wasn't getting very accurate humidity readings so I swapped it for a BME280 in the final version. Eventually I will make a little extension cable for the sensor to move it away from the radiated heat of the light. A 3D printed enclosure (link) holds all the goodies.



Control of the homemade Ebb & Flow system as well as data logging of Temp / Humidity / VPD is run through Node-RED on a Raspberry Pi 2 with a dashboard for at-a-glance status. (sad trombone) You can see the humidity is a little low for my new seedling. The new ventilation system is too powerful even on low speed.

Now grow you little plant, grooooowwww!

Last edited: