stardustsailor
Well-Known Member
Today,I've spend a little more time than usual ,at my grow tent ....
I've noticed more closely the 'effects ' of the CXAs 3070 3000K ...
At ~ 900mA .....And with an average Tc of ~33°C ......
Then some thoughts started to pop-up to my mind ...
One after another ...
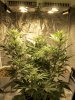
(Pic has been 'resized' and 'sharpened' in Photoshop.)
" Well...That girl seems to really enjoy herself,ledbathing under those Warm White CoBs ..."
" at 900mA ...With Tc 33 Celcious grades ..."
" Yeap,for sure light output here ,is way different than probably in another -hypothetical situation-
where at this exact fixture ,leds would have a Tc of 80 Celcious grades,@900mA .... "
"For sure ,quite a big difference ...."
"So ,in fact two DIY same fixtures using same drivers and same leds/arrays/COBs but different
cooling approach and fan power, possibly will have way different 'effects' on plant growth and productivity .."
" Hmmm...While all the rest are the same being top-notch parts ...Cooling actually is a very crucial complicated 'part' ..."
" That can 'keep in ground' or really 'fly high up to the sky' ,a led light ..."
"it can consist of top-notch materials ....
But ...
..Without those having actually ,the ability to ensure a 100% highly efficient cooling ! "
"Not by themselves,at least ...The whole cooling design must co-operate ,with the top-notch parts ...Otherwise ...."
"Even of inferior quality parts are used ...If the cooling design is excellent ...Cooling should probably be ,evenly if not more efficient that of a system consisting of top quality parts in a bad cooling design ... "
"Ok ..But how one can measure/ determine by numbers the cooling efficiency of a design ? "
" For a given heat power disissipation ,how many "cooling " watts are used to drop x °C ? "
"Like something :
if a cooling scheme A ,dissipating 1W of heat ,using 0.5 Watts of fan power ,is decreasing Tc 10 °C
if a cooling scheme B ,dissipating 1W of heat ,using 1 Watts of fan power ,is decreasing Tc 17 °C
if a cooling scheme C ,dissipating 1W of heat ,using 0.3 Watts of fan power ,is decreasing Tc 7°C
Which is more efficient of three ? "
"Well ,it could stand not by the unit °C/Watt of thermal resistance ,but like a unitless ratio ..
Of the heat power dissipated to fan power used ,in order Tc to decrease 1°C ...."
" I'll ask for help ,at RIU ... "
I've noticed more closely the 'effects ' of the CXAs 3070 3000K ...
At ~ 900mA .....And with an average Tc of ~33°C ......
Then some thoughts started to pop-up to my mind ...
One after another ...
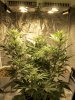
(Pic has been 'resized' and 'sharpened' in Photoshop.)
" Well...That girl seems to really enjoy herself,ledbathing under those Warm White CoBs ..."
" at 900mA ...With Tc 33 Celcious grades ..."
" Yeap,for sure light output here ,is way different than probably in another -hypothetical situation-
where at this exact fixture ,leds would have a Tc of 80 Celcious grades,@900mA .... "
"For sure ,quite a big difference ...."
"So ,in fact two DIY same fixtures using same drivers and same leds/arrays/COBs but different
cooling approach and fan power, possibly will have way different 'effects' on plant growth and productivity .."
" Hmmm...While all the rest are the same being top-notch parts ...Cooling actually is a very crucial complicated 'part' ..."
" That can 'keep in ground' or really 'fly high up to the sky' ,a led light ..."
"it can consist of top-notch materials ....
But ...
..Without those having actually ,the ability to ensure a 100% highly efficient cooling ! "
"Not by themselves,at least ...The whole cooling design must co-operate ,with the top-notch parts ...Otherwise ...."
"Even of inferior quality parts are used ...If the cooling design is excellent ...Cooling should probably be ,evenly if not more efficient that of a system consisting of top quality parts in a bad cooling design ... "
"Ok ..But how one can measure/ determine by numbers the cooling efficiency of a design ? "
" For a given heat power disissipation ,how many "cooling " watts are used to drop x °C ? "
"Like something :
if a cooling scheme A ,dissipating 1W of heat ,using 0.5 Watts of fan power ,is decreasing Tc 10 °C
if a cooling scheme B ,dissipating 1W of heat ,using 1 Watts of fan power ,is decreasing Tc 17 °C
if a cooling scheme C ,dissipating 1W of heat ,using 0.3 Watts of fan power ,is decreasing Tc 7°C
Which is more efficient of three ? "
"Well ,it could stand not by the unit °C/Watt of thermal resistance ,but like a unitless ratio ..
Of the heat power dissipated to fan power used ,in order Tc to decrease 1°C ...."
" I'll ask for help ,at RIU ... "
Last edited: